
PMDX-107 Fwd/Run connects to the FOR terminal on the VFD for Forward. PMDX-107 COM connects to DCM terminal on the VFD for Digital common. PMDX-107 Agnd connects to the ACM terminal on the VFD for Analog common. This is like the wiper on a potentiometer. PMDX-107 Aout connects to the VI (analog voltage in). If you would rather use a controller such as the PMDX-107 to simulate the effect of a potentiometer using the Aref, Aout and Agnd and the Rev/Dir and Fwd/Run terminals to control operation and direction, you can connect those to the VFD. If you want speed control, it is recommended to use the RS-485 connection on the VFD and use the control program such as Mach3 to communication serially with the VFD using this RS-485 connection.
#CNC USB CONTROLLER FIRMWARE DOWNLOAD MANUAL#
Anyway email me a wiring diagram for the PRT 1500 watt spindle motor control box and has the emergency stop on and off switch manual PC and of course yhe screanm the link to add information to this solution: Is there a wiring diagram for hooking up your hex inverter between your USB breakout board and the controller? I can not get anything out of them pertaining help they keep telling me the same thing over and over and over and I'm doing it and send them pictures that I know. I got 6040 1500kw water cold engraver 3 axis from china. Anyway email me a wiring diagram for the PRT 1500 watt spindle motor control box and has the emergency stop on and off switch manual PC and of course yhe screanm Additional Information: I got a question? I am a dummy when it comes to cnc.


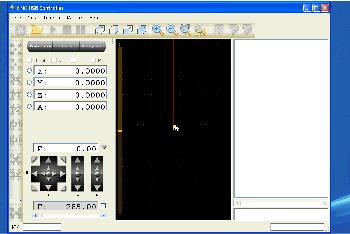
Additional Information: I got a question? I am a dummy when it comes to cnc. Connect the 1Y pin from the hex inverter to the driver. Connect the CW terminal from the USB interface to the 1A pin on the hex inverter. Connect the GND pin from the USB interface to the GND pin on the hex inverter. The pin on the keyboard jog header can be used. First, go to this link and look at the chip diagram: Connect 5V from the USB interface tothe VCC pin. The use of the hex inverter in the application to invert a direction signal to have a motor run in the reverse directions is relatively simple. My pick is that a quality USB cable will fix it though, worked for me.Ĭlick the link to add information to this solution: I have your USB controller sitting here and want to control it with something other than PlanetCNC control software?Ĭlick the link to add information to this solution: I have a planetcnc USB controller to run my project and when I start the 240v router the USB connection shuts down. Alternatively you may need to sheild your limit switch, estop and or motor cabling. In the first instance try to use a quality double sheilded USB cable, hopefully this will fix your problem. Additional Information: Additional Information: Additional Information: The planet cnc controller can be prone to electrical interference and has been known to cause such problems.
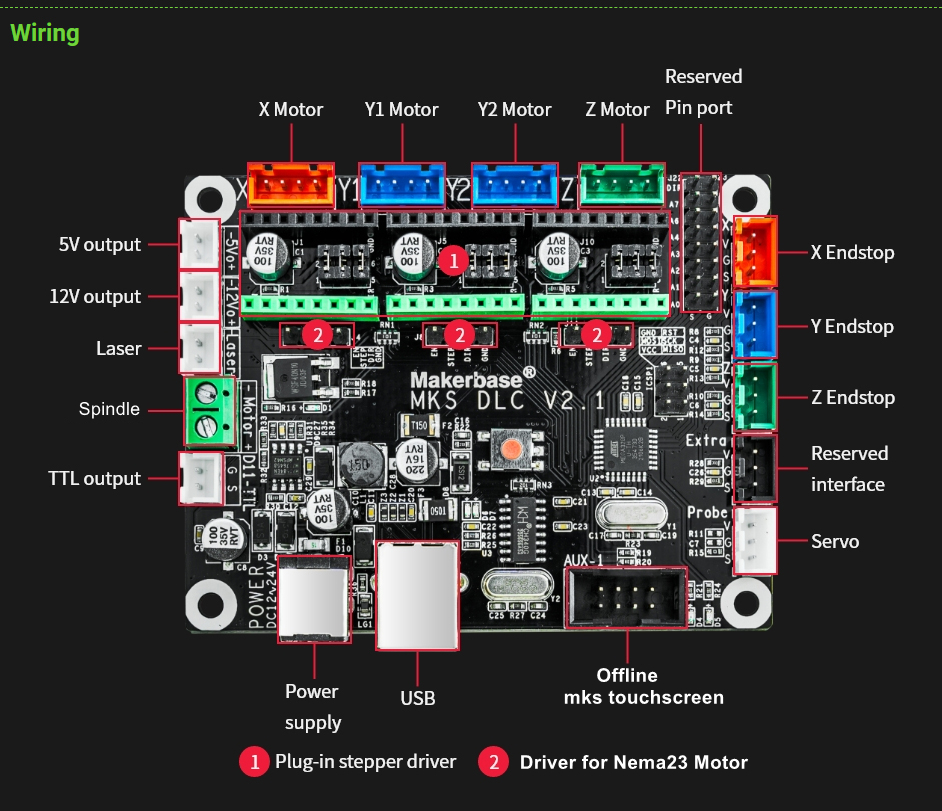
The price combination is much higher than the USB controller with planet-cnc, but will work with Mach3. Second, if you have a laptop, or really want to use the USB as the main interface for controlling the machine, you will need to get the smoothstepper board which works with mach3. If you have a laptop/notebook computer, this will not be possible. There are two main alternatives if you want to use the mach3 software: First, get a parallel port card and add it to your computer and get a parallel breakout board.
#CNC USB CONTROLLER FIRMWARE DOWNLOAD SOFTWARE#
The planet-cnc software delivers instructions to the microcontroller on the board and the microcontroller will send out the pulse trains needed to move the machine correctly. This software is well made and will provide great functionality. The USB controller will only work with the Planet-CNC software.
